プラスチック製品は、包装、建設、電子機器、消費財など、幅広い業界で広く使用されています。成形技術は様々ですが、一般的な製造プロセスは主に以下の段階を踏みます。
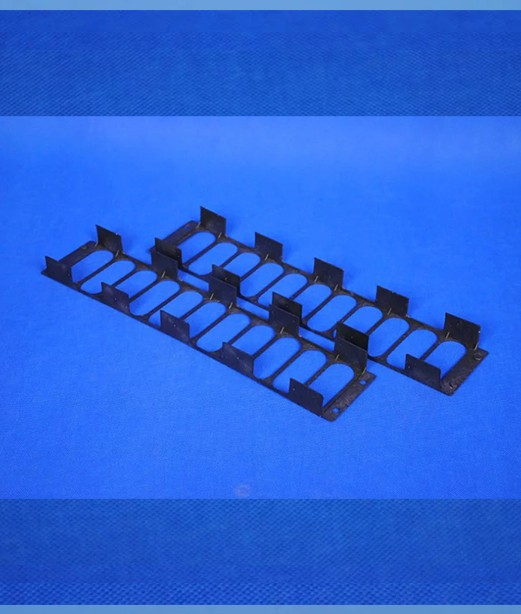
1. 原材料の準備
プラスチック材料には主に熱可塑性プラスチック(例: 体育, PP、PVC、PS、ABS、PC)および熱硬化性樹脂。これらは通常、顆粒または粉末の形で供給されます。
- 特定の特性を強化するために、可塑剤、安定剤、充填剤、難燃剤、顔料などの添加剤を組み込むこともできます。
- 通常、加工前に材料は乾燥され、水分が除去され、気泡や銀色の筋などの欠陥が防止されます。
2. 可塑化と溶融
プラスチック原料は、特殊な装置(射出成形機や押出機など)で加熱・剪断され、粘性のある溶融状態になります。この工程は、材料を成形するための準備として非常に重要です。
3. 成形方法(製品の種類によって異なります)
製品の要件に応じて、さまざまなプラスチック成形技術が使用されます。
- 射出成形 – 溶融プラスチックを金型キャビティに注入します。家電製品のハウジングや自動車部品などの複雑な部品に適しています。
- 押出成形 – プラスチックをパイプ、シート、フィルムなどの形状に連続的に成形します。
- ブロー成形 – 金型内で熱いプラスチックパリソンを膨らませて、ボトルなどの中空部品を作るために使用されます。
- カレンダー加工 – 加熱ローラーの間で溶融プラスチックを圧縮してシートまたはフィルムを製造します。通常は PVC フィルムに使用されます。
- 熱成形(真空成形) – 加熱されたプラスチックシートが真空を使用して金型上で成形されます。包装トレイでよく使用されます。
- 回転成形、発泡成形など – タンク、フロート、断熱材などの大型または軽量の製品に使用されます。
4. 冷却と脱型
製品が成形されたら、最終形状を維持するために冷却する必要があります。冷却方法は、工程に応じて空冷から水冷まで様々です。冷却後、製品は金型から取り出されます。
5. トリミングと後処理
成形部品にはバリやバリが発生する場合があり、これらを除去する必要があります。製品設計に応じて、溶接、穴あけ、印刷、組み立て、熱処理などの後加工が必要となる場合もあります。
6. 品質検査と梱包
完成品は、寸法、表面外観、機械的特性などについて品質検査を受けます。合格品はラベルを貼付し、梱包の上、保管または出荷されます。